How Does Plastic Extrusion Work?
- siliconeplastics
- Jun 5
- 3 min read
Plastic extrusion is a fascinating process that transforms raw plastic materials into usable products. It plays a vital role in manufacturing across various industries, especially in plastic production hubs like Utah. In this FAQ, we'll break down the steps of plastic extrusion in an easy-to-understand way.
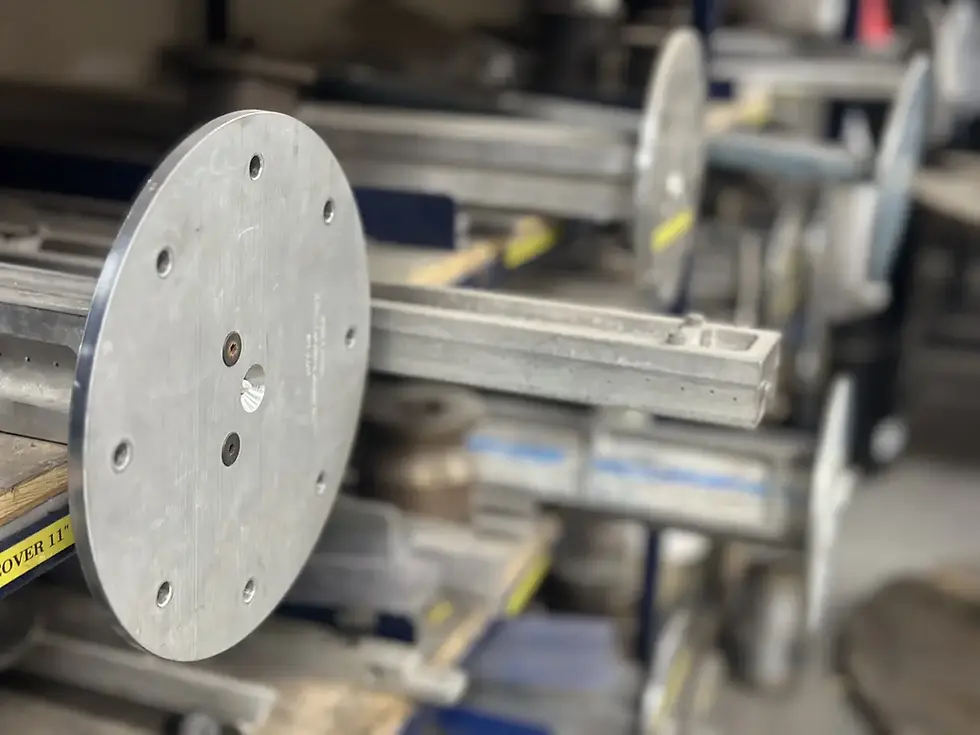
What is Plastic Extrusion?
Plastic extrusion is a manufacturing process that involves melting plastic pellets and forming them into continuous shapes, such as sheets, tubes, or profiles. This process is essential in creating a wide variety of plastic products.
In essence, plastic extrusion is about reshaping raw material into something useful. This transformation occurs at high temperatures, where pellets are heated until they become a viscous liquid. This state allows for easy shaping and molding.
What’s interesting about plastic extrusion is its ability to produce items of varying complexity. From simple plastic sheets used in packaging to complex shapes found in automotive parts, the process is versatile and adaptable.
The Extrusion Process Explained
The extrusion process typically starts with feeding plastic pellets into a hopper, where they are heated and melted before being pushed through a die to form the desired shape. Understanding each stage helps demystify how raw materials become finished products.
After the pellets reach the die, they are shaped as they exit, which ensures uniformity. This part of the process is critical because even minor discrepancies can impact the quality of the final product.
Cooling is another vital stage. Once the molten plastic exits the die, it needs to cool quickly to retain its shape. This can involve air cooling or immersion in water, depending on the type of product being made.
Next is the cutting phase, where the extruded material is cut into manageable lengths. This is often done while the material is still warm, making it easier to work with. The entire process from start to finish creates a continuous flow, ensuring efficiency.
Key Components of Extrusion Equipment
Various components are involved in plastic extrusion, including the extruder, die, cooling system, and cut-off devices. Each part plays a crucial role in ensuring the efficiency and quality of the final product.
The extruder is the heart of the operation, responsible for melting the plastic pellets and forming them into shapes. Its design allows for precise control of temperature and pressure, which is paramount in achieving the desired consistency.
Equally important is the die, which shapes the molten plastic. Different dies can create different profiles, meaning that versatility is built into the extrusion machine. This allows manufacturers to produce a wide range of products.
The cooling system ensures that the extruded shape retains its form as it hardens. Without effective cooling, the shape could warp or not form correctly, leading to wasted materials and time.
Lastly, the cut-off devices work to slice the extruded product into the desired lengths, ensuring that what emerges meets manufacturing specifications. Together, these components create a seamless flow of production.
Applications of Extruded Plastics
Extruded plastics are used across numerous industries, from construction to automotive and consumer goods. This section highlights popular applications and showcases the versatility of plastic extrusion.
In the construction industry, plastic extrusions can be found in window frames, siding, and various fittings. They provide durability and weather resistance, making them indispensable materials for modern buildings.
Similarly, the automotive industry relies on extruded plastics for components like dashboards and trim pieces. These parts not only reduce weight but also enhance the vehicle's aesthetics and functionality.
Consumer goods also utilize extruded plastics extensively. From tubing used in kitchen products to specialty packaging materials, the applications are virtually endless, showing just how integral plastic extrusion is to our daily lives.
Benefits of Plastic Extrusion
Plastic extrusion offers several advantages, including cost efficiency, scalability, and the ability to produce complicated shapes. We'll explore why many manufacturers prefer this method over others.
One significant benefit of extrusion is the low production costs, especially when creating high volumes of products. As machinery runs continuously, it maximizes output while minimizing labor expenses.
The scalability of the extrusion process makes it appealing for businesses of all sizes. Manufacturers can easily adjust the scale of production, which is perfect for responding to market demands without the need for extensive reconfiguration.
Furthermore, the capacity to create unique, custom shapes means that companies can develop specialized products that stand out in the marketplace. It gives businesses an edge when compared to standard manufacturing methods.
Wrapping Up the Plastic Extrusion Process
By understanding the plastic extrusion process, you can appreciate the complexity behind the plastic products we encounter every day. Whether you're in manufacturing or simply curious, knowing the basics can enhance your knowledge of this crucial process.
Comments